Funktionsweise
Das Induktivhärten gehört zur Gruppe des Randschichthärtens und wird auf speziellen Maschinen, die mit Hochfrequenz- oder Mittelfrequenz-Generatoren ausgerüstet sind, durchgeführt.
Funktionsweise
Das Induktivhärten gehört zur Gruppe des Randschichthärtens und wird auf speziellen Maschinen, die mit Hochfrequenz- oder Mittelfrequenz-Generatoren ausgerüstet sind, durchgeführt.
Induktive Oberflächenhärtung
Mit der Härtemaschine wird der zu härtende Bereich für die induktive Oberflächenhärtung eines Bauteils abgefahren. Dies geschieht heute meistens über eine CNC-Steuerung. Hier werden die Härteparameter wie Leistung des Generators, Vorschubgeschwindigkeit, Haltezeiten und Abschreckbrausenzeiten programmiert. Zudem werden heute oft wichtige qualitätsrelevante Parameter wie Härtetemperatur oder Leistungsabgabe sowie die Abschreckmittelmenge überwacht. Somit kann für jedes gehärtete Teil eine korrekte Härtung nachgewiesen und die Rückverfolgbarkeit sichergestellt werden.
Beim Induktionshärten werden durch einen mit Wechselstrom durchflossenen, wassergekühlten Induktor, der das zu härtende Bauteil umschließt, Wirbelströme erzeugt. Diese bringen die Oberfläche des Werkstückes, je nach Frequenz des Generators, unterschiedlich tief auf die werkstoffbedingte Härtetemperatur. Es erfolgt eine sofortige Abschreckung, die verantwortlich für die Martensitbildung im Randbereich und somit für die Randschichthärtung ist.
Die Frequenz des Wechselstromes beeinflusst die Einhärtetiefe entscheidend. Je höher die Frequenz ist, desto geringer ist die Einhärtetiefe.
Induktives Anlassen und Löten ist ebenfalls möglich.
Mit der Härtemaschine wird der zu härtende Bereich eines Bauteils abgefahren. Dies geschieht heute meistens über eine CNC-Steuerung. Hier werden die Härteparameter wie Leistung des Generators, Vorschubgeschwindigkeit, Haltezeiten und Abschreckbrausenzeiten programmiert. Zudem werden heute oft wichtige qualitätsrelevante Parameter wie Härtetemperatur oder Leistungsabgabe sowie die Abschreckmittelmenge überwacht. Somit kann für jedes gehärtete Teil eine korrekte Härtung nachgewiesen und die Rückverfolgbarkeit sichergestellt werden.
Beim Induktionshärten werden durch einen mit Wechselstrom durchflossenen, wassergekühlten Induktor, der das zu härtende Bauteil umschließt, Wirbelströme erzeugt. Diese bringen die Oberfläche des Werkstückes, je nach Frequenz des Generators, unterschiedlich tief auf die werkstoffbedingte Härtetemperatur. Es erfolgt eine sofortige Abschreckung, die verantwortlich für die Martensitbildung im Randbereich und somit für die Randschichthärtung ist.
Die Frequenz des Wechselstromes beeinflusst die Einhärtetiefe entscheidend. Je höher die Frequenz ist, desto geringer ist die Einhärtetiefe.
Induktives Anlassen und Löten ist ebenfalls möglich.
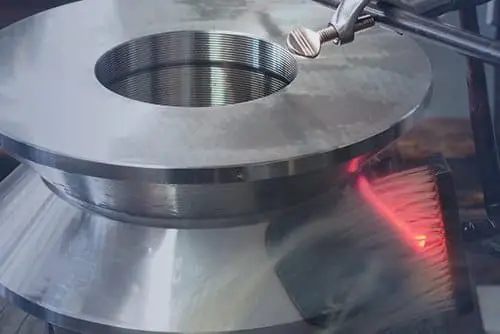
Welcher Stahl eignet sich zum Induktivhärten?
Voraussetzung für die induktive Oberflächenhärtung ist die Verwendung eines Stahles, der zum Erreichen der geforderten Härte ausreichend Kohlenstoff enthält.
Grundsätzlich sind vorvergütete Stähle, wie z.B. der 42CrMo4+QT am besten geeignet, da hier eine gleichmäßige Verteilung der Legierungsbestandteile im Gefüge vorhanden ist. Vergütungsstähle ab einem Kohlenstoffgehalt von 0,35% erreichen eine deutliche Härteannahme. Aber auch rostfreie und Kugellagerstähle wie z.B. der 100Cr6 sowie Grauguss und Temperguss mit einem perlitischen Grundgefüge und feiner Graphitausbildung sind ebenfalls geeignet. Dies gilt auch bei Einsatzwerkstoffen im aufgekohlten Zustand.
Zur weiteren Information empfehlen wir Ihnen die DIN 17212 (Stähle für Flamm- und Induktionshärten).
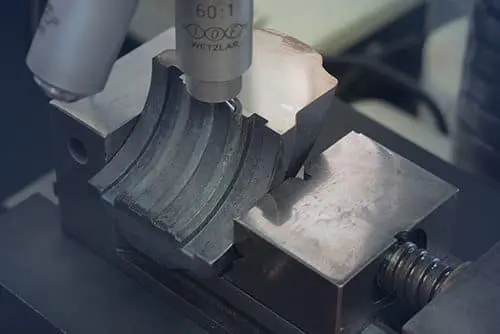
Vorteile des Induktivhärten
- Nur die Verschleißbereiche werden gehärtet
- Bauteile können partiell geglüht werden
- Maß- und Formänderungen sind im Allgemeinen gering
- Nachträgliches Richten ist möglich
- Nacharbeitskosten geringer
- Eine harte Randschicht und ein zäher Kern wird erreicht
- Hohe Reproduzierbarkeit durch CNC gesteuerte Härtemaschinen
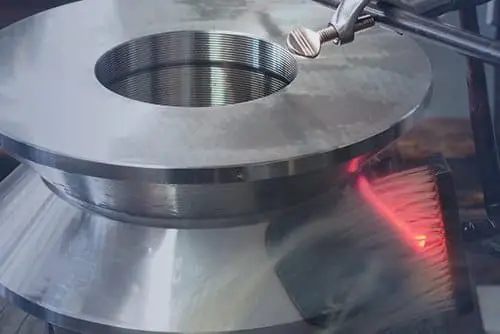
Welcher Stahl eignet sich zum Induktivhärten?
Voraussetzung ist die Verwendung eines Stahles, der zum Erreichen der geforderten Härte ausreichend Kohlenstoff enthält.
Grundsätzlich sind vorvergütete Stähle, wie z.B. der 42CrMo4+QT am besten geeignet, da hier eine gleichmäßige Verteilung der Legierungsbestandteile im Gefüge vorhanden ist. Vergütungsstähle ab einem Kohlenstoffgehalt von 0,35% erreichen eine deutliche Härteannahme. Aber auch rostfreie und Kugellagerstähle wie z.B. der 100Cr6 sowie Grauguss und Temperguss mit einem perlitischen Grundgefüge und feiner Graphitausbildung sind ebenfalls geeignet. Dies gilt auch bei Einsatzwerkstoffen im aufgekohlten Zustand.
Zur weiteren Information empfehlen wir Ihnen die DIN 17212 (Stähle für Flamm- und Induktionshärten).
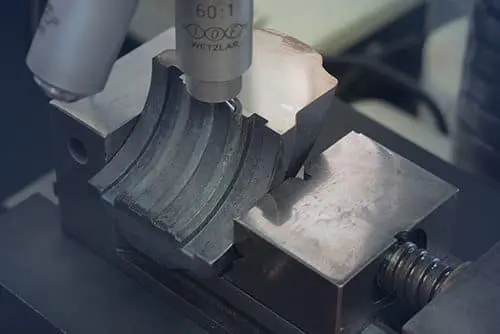
Vorteile des Induktivhärten
- Nur die Verschleißbereiche werden gehärtet
- Bauteile können partiell geglüht werden
- Maß- und Formänderungen sind im Allgemeinen gering
- Nachträgliches Richten ist möglich
- Nacharbeitskosten geringer
- Eine harte Randschicht und ein zäher Kern wird erreicht
- Hohe Reproduzierbarkeit durch CNC gesteuerte Härtemaschinen